可持续发展的理念对于我们的运营至关重要。把可持续发展的理念融入运营可以确保沙特阿美未来的长期蓬勃发展,并能够保持世界级能源化工一体化公司的地位。
可持续发展使公司在日常运营的同时,将社会和环境影响纳入充分考虑。这一理念也是我们制定战略助推全球能源转型和向低碳经济转型的关键驱动力。
我们认识到气候挑战的规模和紧迫性。我们正在利用我们的运营优势和业务组合,在能源转型中发挥我们的作用,我们的雄心是到 2050 年实现我们全资运营资产的净零排放,同时开发低碳能源解决方案。这一计划符合沙特到 2060 年实现净零排放的目标。
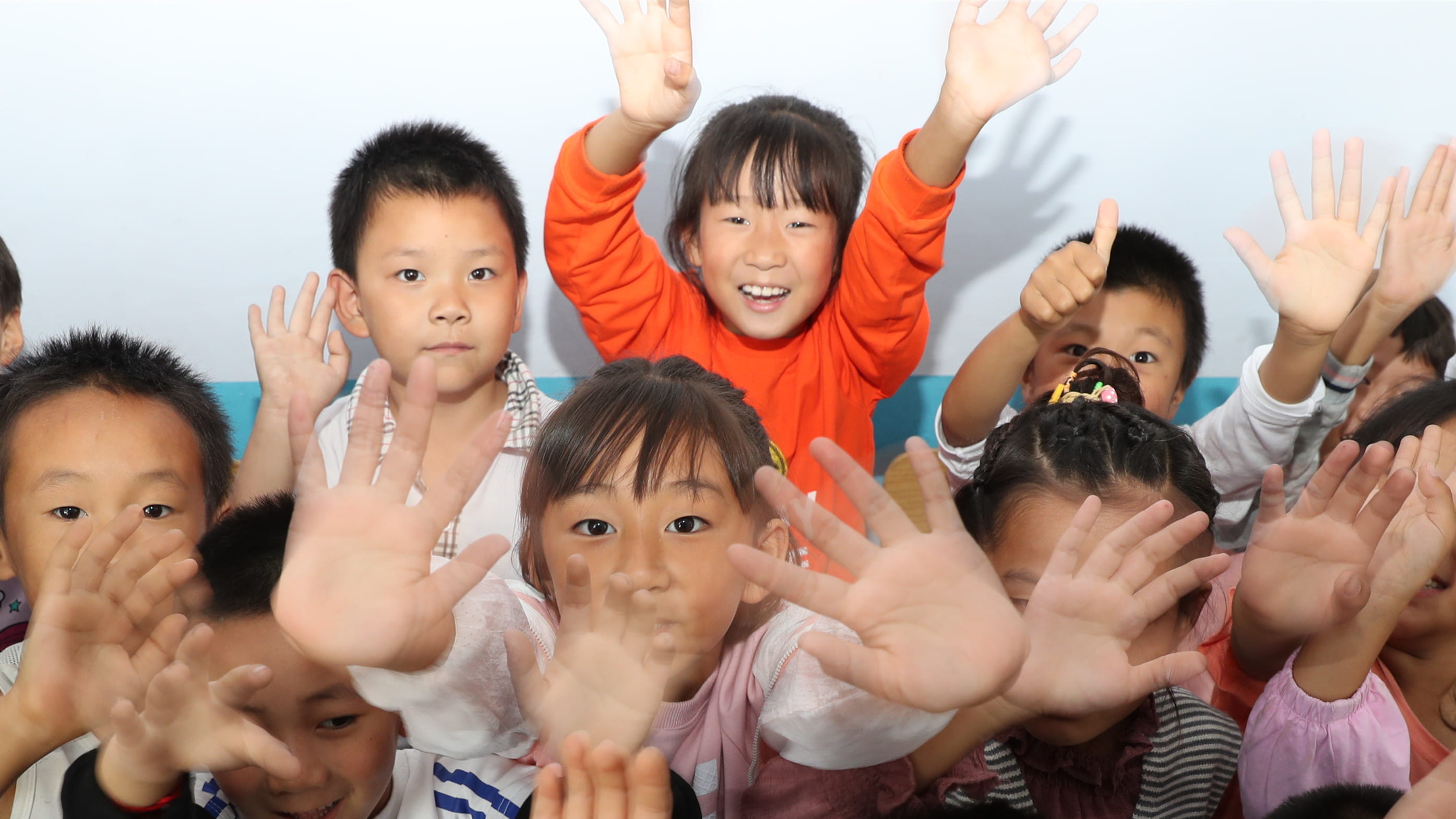